|
Post by DeadlyPeace on Sept 16, 2005 10:34:04 GMT -5
I'm looking to build a Mobil TRI ramp sometime in the future. I want to make it so that it can be torn down when not in use and so that one person can put it together quickly (About 10-15 minutes) and easily. Here's the design I have for it so far.
 It's 2'x14' and 20 degrees. I also want to make it adjust able to 30 degrees.
The axle and/or tire would be (easily) removed with the help some type of built on jack. This will will depend on what type/shape axle I end up using. Probably some kind of trailer axle. At the front where the ramp and the base come together I'm going use heavy duty hinges.
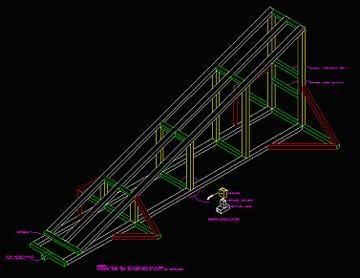
Here's the idea I have for the lower half of the vertical braces. I've come up with a couple different ideas for the upper half of the brace for connecting to the ramp, but nothing in stone yet. For the angle adjustment I was thinking of doing basically the same thing at the top too, but it will need to pivot some how too. Don't want to use hinges for this. I thought I'd see if any body had any good ideas out there for this or any other part of the ramp.
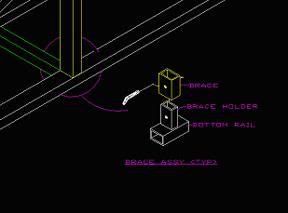 Throw out your thoughts. Good, bad or indifferent. TIA.
DP
|
|
|
Post by 94cnytoy on Sept 16, 2005 13:20:51 GMT -5
Just a few thoughts... 1) Rear axle/wheel set on leg-downs (similar to a log splitter set-up, if you have any trees left out there..ha,ha,ha). The leg-down would allow self containment and individual movement. It would be attached to a sleeve or something to allow for rotation.Of course, this idea shits the bed if you need suspension..... 2) I wouldn't bother hinging the front with an actual pinned hinge, as the arc is so small. That can be done with a simple pinned box-tubed bracket. But, for off the shelf parts, a set of galvanized strap hinges would last for years. But 2-pieces of angle iron on either side of the upper frame rails with a pin or bolt would suffice. 3) Realistically, the four boxed supports you show could all be hinged and pinned. The upper rail would have alternate inclination/slope holes and would all follow the same sloped pattern as necc. You would obviously, have to make the upper platform longer to accomodate this. If spaced properly, they could fold down among themselves, if the first(lowest) hing point were blocked and raised.
My questions are this. Is there actual set standards for RTI ramp width and length??? How far do you intend on haulin this around?
PM me with your e-mail address if you want to see any examples of my idea's. I will have to draw and scan them from my work computers.
You know, I will no longer sleep at night until you build this...
Stew
|
|
|
Post by DeadlyPeace on Sept 17, 2005 3:28:39 GMT -5
Welcome to my world of insomnia ;D I'm alway up and thinking about 20 to 30 products/mods a head. Right now I'm in the process of building an under bed tool box. I've got the box pretty much done, now I'm just waiting for a time to bob the off the tail so I can do the rest.
A leg down axle is what I was thinking of using, but with the legs going up so I could just remove the tires if I couldn't find a way to do a simple disconnect of the entire axle. And suspension is not an issue. Had no plans on added it. Figured the tires will be all the suspension it will need. It won't be going on any long tows. Maybe 75 miles at the most.
The hinges for the front I was going to actual make from solid steel rods and pipe.
I thought of using angle iron for the braces to the top rail, but decide to use channel instead. Just been trying to think of the best way to make them pivot so they'll sits flat on the square tube steel on the top rail. My best idea so far is doing a steel pipe and solid rod type hinge with holes drilled at certain angles for when the ramp angle is adjusted.
I thought about hinging the bottom of the support braces, but went against it when they'd end up laying on top of each other. After posting the original idea I started thinking about the braces mounts and that I didn't want to do it cuz I want the top rail to lay down as flat as possible on the base. So I started thinking about doing some kind of removable hinge for them. Just haven't worked out the details for it yet.
Not that it make that much difference, but I would like to make it bolt free so it just uses pins for a tool free setup.
There are no real standards for the length and width. I've seen them as short as 6' and as long as 15'. The only real standard is the angle.
94cnytoy I'll PM you my addy.Ramp Travel Index (in case anyone needs to know)
RTI is a way of measuring your vehicle's ability to flex. It is measured by how far up a ramp (standard is 20 degrees) the vehicle can go while still keeping all four tires in contact with the surface underneath. Variables such as vehicle length, suspension, and so on are compensated for by using the following equations: The number of inches a vehicle travels up the ramp before running out of suspension travel (when a tire leaves the ground), divided by it's wheelbase. Then multiply that figure by 1000. A perfect score would be 1000, that is, the vehicle can go as far up the ramp as its wheelbase without lifting a tire. Well modified rigs can reach and exceed that depending on how much customizing has been done. To compensate for extreme machines, a 23-degree and even a 30-degree ramp have been used. The calculations are the same, just be sure to mention which standards you're using when you brag.
Simplified: Inches Traveled divided by Wheelbase, multiply by 1000, equals RTI
This for example is not the right way to check your RTI [edit] This wasn't the orriginal pic I used, but it seemed to have stopped working and I couldn't remember or find the site I got it from. So I decide to replace it with Snorkleman's honda RTI ramp.
|
|
|
Post by 94cnytoy on Sept 19, 2005 10:19:33 GMT -5
Could you please change the title to RTI ramp. "Travel Ramp Index" is driving me crazy..... Stew
Unless your insinuating "Traveling Ramp Innovations"
|
|
|
Post by Hoodlum on Sept 19, 2005 12:40:34 GMT -5
Welcome to my world of insomnia
Great idea DEADLY I did have a input but 94 cnytoy covered it 1) Rear axle/wheel set on leg-downs (similar to a log splitter set-up, if you have any trees left out there..ha,ha,ha). The leg-down would allow self containment and individual movement. It would be attached to a sleeve or something to allow for rotation.Of course, this idea shits the bed if you need suspension..... so good luck! and def keep us posted.
|
|
|
Post by Hoodlum on Sept 20, 2005 9:03:57 GMT -5
What about using sring loaded lock pins(used on some swing arms to lock them in place) with another safety pin to keep them in position(just added safety)
|
|
|
Post by 94cnytoy on Sept 20, 2005 10:25:03 GMT -5
Thanks for the title change, I feel much better....
My growing concern with all these pinned or hinged joints is stability. I guess you won't really know until its together.... But, we are talking about substantial vertical, horizontal and trapazoidal loads.... I'm guessing all these braces will be "H" brackets connecting to the main frames, or at least they'd have to be for stabilization purposes for full sandwiched pinned connections. No big deal though.
Deadly.... What are you plannning for the tire surface material? Extruded or something else... It's be nice if you could find a catwalk off of some industrial stuff(USED=CHEAP)
Ya'know, it doesn't look bad for a solid unit either... How bad is your storage situation??? Stew
|
|
|
Post by DeadlyPeace on Sept 20, 2005 10:34:34 GMT -5
Just came across this while looking for other ideas. Check out the 2nd and 3rd to last pics of the axle setup. I think it's a great idea and would be cheaper to build then buying an axle. Just need to find a way to innervate it into my collapsible idea. What do you guys think? www.socalbigdawgs.com/gallery/view_album.php?set_albumName=Big-Dawg-RTI-Ramp
Hoodlum The spring pins are a good idea. Might not be needed, but might be good for the hold down pins during tows.
94cnytoy The braces would be more of a upside down U shape. As for as the pins and hinges I think it should do fine. If not I can alway add a little more bracing if needed. Or just full out weld it solid if it comes to that. Storage isn't a problem. It just makes it easier to store and tow, and I think the most important (driving factor) to this idea is cuz no one has made collapsible one yet that I know of.
For the tire surface material, extruded is what I had in mind and very common for most RTI ramps.
|
|
|
Post by Hoodlum on Sept 20, 2005 10:54:25 GMT -5
How bad is your storage situation DEADLY seems to have a black hole of sort for storage he's the only one I know has more stuff than I do. LOL
|
|
|
Post by DeadlyPeace on Sept 20, 2005 11:17:45 GMT -5
Hoodlum, does that mean we're REDNECK? I did mow the lawn the other day and found my dog that was missing for the past month ;D LOL ;D
|
|
|
Post by Hoodlum on Sept 20, 2005 12:03:32 GMT -5
Hoodlum, does that mean we're REDNECK? I did mow the lawn the other day and found my dog that was missing for the past month LOL
FOFLAO!! and if we're not REDNECK then we really screwed something up big time.Other than loosing a few pounds is your dog o.k. LOL The only thing I'm missing is the motor hanging from the tree by the garage. And by the way did you pay snorkleman for the license fees for using his pic. ;D
|
|
|
Post by 94cnytoy on Sept 20, 2005 18:58:06 GMT -5
Well, I scatched my head for a few hours today (working?).... The 2 different angles are killing me... Yeah, I know, makes you feel good right? No matter how I do the match, the legs can't be folding and multi-level. They'd have to be interchangeable. To swing a 10* arc for the upper to lower pitch, they'd be too far over to properly support the upper frame. They would have to be moved out to the next pin set(lower also) to accomplish the lower pitch and the longest set aside. How about this... The bottom rail would be drilled and marked for different staging of the pins and support. Essentially, it would be a rail with pin sets just like an engine hoist.(which by the way could be the lifting assy?  ). This would allow the supports to maintain the full height and near plumb support at all times. The longest support eliminated at the lowest pitch( yes I'm redundant). The bottom of the support brackets could them be crossed braced and have a longer connection channel to the base channel creating more stability. Yeah, I know, draw it.... I sketched something today, but screwed it up.. I ran 14* and 20* 20* and 30* is WORSE!!! By the way, that link is a damn fine wheel system. Must have been carni's in their past lives. Nothin against carni's, they just scare me... I work alot better with tools and stock in hand. Sooooo many things work (or don't) on paper. Just send me the stuff, I'll figur it out. I grew up putting motors ON thing (notice I said on, not in). My parents have a lovely 12Hp 60 gal porc., claw foot bath tub. (didn't want to push it back up the hill for the races) By any chance have you already started this? You talk as though you've cut something(metal, not flesh) Stew
|
|
|
Post by DeadlyPeace on Sept 21, 2005 10:19:34 GMT -5
FOFLAO!! and if we're not REDNECK then we really screwed something up big time. I've screwed a lot of things up in my time, but I always had some else to blame it on. And good friends for witnesses that were willing to lie for me. ;D LOL ;D
Other than loosing a few pounds is your dog o.k. LOL He was ok till I found with the mower. Now my neighbor's in jail for killing my dog.
And by the way did you pay snorkleman for the license fees for using his pic. ;D The checks in the mail?? ;D
94cnytoy, draw it up LOL Are you talking about the base sliding or the braces sliding? My idea for adjusting the angle was to have a square tube within another square tube like a engine hoist (or bumper hitch for what I had i mind) with the two longest ones having two holding pins and the shorter two with one. When they pivoted forward they would only need to go 4.5* per angle change. Angles being 20*, (23*), 25*, and 30* (23* is normally the next angle up, but I left it out of my calculations. Figured if I could get the rest then I should be able to get 23*). At the 30* angle the longest brace would only need to extend about 2'-3" and have a lap between the two pieces of about 2'-6". Now thinking about it, what if I made the base slide also so that it pulls the bottom end in to re-plumb the braces after adjusting them.
For the bottom of the braces I was thinking of rounding the front edge just enough to let the braces pivot into the furthest position. It would then fit over (around) another short piece of square tube with the top also rounded just enough for the pivot. Then a pin through both of them to act as the hinge.
BTW no I haven't started on this yet. Got a few mods to do on my rig first. This might just be the next project. I'm guessing that I have about a month or so to let the gears grind and smoke. ;D
|
|
|
Post by rockcrawlintoy on Sept 21, 2005 12:04:51 GMT -5
the ramp we built was not movable. it was about 5.5 feet tall and about 18-20 inches wide. it was also built at a 30 degree angle. seems like a steep ramp but my toyota could almost get to the top when backing up we should have made it a little longer. also dont build a 20 degree rampa truck with just a little flex will be be able to max it out
|
|
|
Post by 94cnytoy on Sept 21, 2005 16:31:52 GMT -5
The bottom braces slide/move is exactly what I'm saying. Rounding the bottom or any end that pivots would have to be done too. My intentions are for a solid base frame. Movin legs.
Not that I've ever done simple math wrong...... 20* is about 4.5'' per foot rise 30* is about 7'' per foot of rise. Keep in mind that your working on a plane, from an arc. If you take the longest leg, installed vertical at full height of the 20* ramp (63'' of total rise for the 14'0'' run). It would have to accomodate a 35'' height difference.(14'-0'' run x 7'' ft = 98'' total - 63'' = 35'') The tallest support leg would be at almost 45* angle at 20*(with the base in the original position)
Got any spare lumber left from the construction days??? Nothing a few carriage bolts and some 2x4's can't solve. Stew
PPPPS: This beats the sh*t out of residential constr.
|
|
|
Post by DeadlyPeace on Sept 22, 2005 11:07:42 GMT -5
Not stepping on toes…. Rockcrawlintoy if your toy could almost clear your ramp at 30* then you should be about to near clearing my ramp at 20*. Plus that's with your rear tire. What about the front tire? Or maybe that was with the front tire. If your Toy like mine, that sounds to be more correct, but it’s hard to tell without any punctuation.
If you think about it, if your ramp is 30* and 5’-6” then it would be about 9’-6” long. With mine at 20* you’ll still have another 4’-6” of ramp to travel bringing you to a height of 5’-2”. In reality the degrees don’t matter, it’s the height. For example if you want you could use a fork lift and lift one tire and get the same results. Plus just because our Toys can clear it does mean all of them will. Also when working on them I like to see and let the person I’m doing it for see the difference. A 20* ramp makes it easier for a stock Toy.
And just to mention, that's way I’m making it ADJUSTIBLE up to 30* (maybe even 35*) and at a fair length. Work on getting your Toy to clear 7’-4”. That’s quite a distance for a tire to be off the ground a still leaving the other three on the ground. I know a few people that can come close to clearing that, and with their front tire. Of course they have larger tires and full axles too.
|
|
|
Post by snorkleman on Sept 24, 2005 12:55:21 GMT -5
I got that check in the mail. I was able to buy that pack of gum i always wanted!
Would it be possible to have the main upright braces tilt forward towards the entrace of the ramp? Instead of using 45 degree square joints use square tube attached to round tube that is mounted but can rotate the braces so the angel of the ramp would increase. Just a thought. Not sure how much you could get in height before the anlge of the braces wouldn't support the weight efficiently. At least this way you wouldn't have to add anything to the ramp except adjust the points where the braces attach to the ramp. I guess you could use pins with different slot holes in the ramp to make the adjustments.
Or you could go ghetto and hook up some air bags or hydraulics to the ramp. Oh yeah hydraulics! Maybe use some pearl metal flake paint on it too! Chrome Dubs for wheels would also be nice. One blingin RTI ramp!!
|
|
|
Post by DeadlyPeace on Sept 27, 2005 20:21:07 GMT -5
Snorkle, glad the check made it to you. I know you’ve been looking forward to reading those Bazooka Joe comics.
Could you sketch me something out of what you’re thinking of? I believe you’re talking about the side braces and it sounds like a workable idea. I haven’t been too worried about the side braces much so no real thought has gone into them yet. Figured it wouldn’t be too hard to work something out for them when I got the rest designed out.
{edit} After some enlighting advice from 94cnytoy and Hoodlum I have decided to remove this information. Maybe some day you;ll be able to see it in full opperation.
DP
|
|
|
Post by 94cnytoy on Sept 28, 2005 10:42:54 GMT -5
Why are you designing houses?
Anyway, so these are self-enclosing inner-outer sleeved tubes correct? or are they removable sections? You'll have to have fairly strong pins with a high shear value, prob like 30k. (impact resistance).
I wouldn't display too much more exact info.. I think your on your well on your way to a patent!
Stew
|
|
|
Post by Hoodlum on Sept 28, 2005 11:56:31 GMT -5
I agree with 94cnytoy after looking this whole project over(for a very long time) you just may as well be on your way to something . keep after it 
|
|